Five-Axis Machining With Delcam's PowerMILL Boosts Danish Tool And Machine Maker
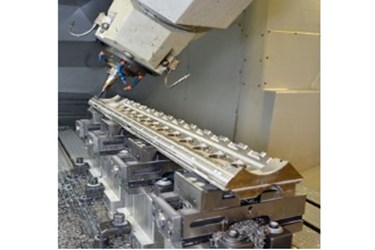
A new five-axis FPT Dino machining centre programmed with Delcam’s PowerMILL CAM system means that Aarestrup Vaerktoejs- og Maskinfabrik (AA-VM) is now able to machine large parts with very complex geometry both quickly and accurately. The company, which is located in the Northern Jutland town of Stoevring, was previously only able to do three-and four-axis machining.
Aage Andersen founded the company in 1983 in the village of Aarestrup as a tool factory for cutting and punching. Ten years later, part of the company moved to Stoevring. A year after that, the company expanded the new location and shut down the branch in Aarestrup. In 2004, the current owner, Kenneth Andersen, took over as new CEO of the company.
Today, the company’s fifteen employees develop, manufacture and optimise tools for punching and forming, and moulds for injection moulding and blow moulding. In addition, the company develops and manufactures spare parts, specialised parts in small numbers and prototypes, as well as special machines developed in close collaboration with its customers. The company’s CNC machinery includes six milling machines and one lathe, as well as two wire-EDM and two sinker-EDM machines.
"We invested in the five-axis machine combined with PowerMILL mainly because we have a number of customers in the food industry that need large and highly complex new parts and replacement parts made to a very high quality,” explained AA-VM CEO, Kenneth Andersen,.
The machining centre is such a huge size that AA-VM had to acquire a neighbouring property to make room for it. The machine can process parts with a length, width and height of up to 3,000 x 1,600 x 800 mm. It uses five-axis simultaneous machining, which allows for faster processing of complex geometry at extremely high precision.
With the introduction of the new machine, it became necessary for AA-VM to upgrade its existing CAM software. This system could not handle the really complex parts required by a number of customers or take advantage of the new machine’s capabilities, according to Mr Andersen. "We examined a number of CAM programs and chose PowerMILL because we rated it as the best solution,” he stated. "We are really happy with the software. We particularly like having Delcam Denmark available to provide professional support and service locally and we are very pleased with that relationship. Another big advantage for us is that, if it becomes necessary, the local Delcam office can provide us with access to the experts at Delcam’s headquarters.”
"PowerMILL is very sophisticated software which can handle virtually any task we can imagine,” added Bjørn Krogh, head of the machining department at AA-VM. "Our three CAM operators are now learning how to use templates and macros in PowerMILL to further optimise the programming process for our toolpaths.”
It has taken AA-VM some time to become familiar with all the advanced possibilities offered by the FPT machining centre but, after less than a year, it is running five to six days a week for the production of newly-developed parts. It has proved particularly beneficial for large moulds where the use of five-axis machining has cut the number of machine set-ups in half, reducing the overall machining time considerably.
The vast majority of the designs for new parts are received from customers as 3D files generated in their different CAD systems. "It is a major advantage for us that, in most cases, we are able to manufacture using the customer’s 3D files directly without further need for editing,” explained Mr. Krogh. "In a few cases, it has been necessary to use Delcam’s PowerSHAPE design software to generate extra geometry such as clamping surfaces.”
Source: Delcam