Acu-Rite MillPWR Control Prompts Consort's Move Into 3-D Contour Machining
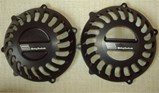
By upgrading from two-axis CNC to a three-axis Acu-Rite MillPWR control system, not only can Consort Precision Engineering leave its Bridgeport knee mill to run unmanned, but the new CNC technology has also opened the door for the introduction of three-dimensional contour machining.
Based in Lowestoft, Consort provides precision machined components to UK customers in the oil/petro-chemical sector as well as being a specialist in the replacement of obsolete parts required by classic motor cycle enthusiasts.
Throughput generally involves batches of 25 components, though one-offs are usual. All materials are processed, including the often problematic Inconnel and titanium.
To keep up with the growing order book, the company's armoury of machine tools includes CNC and manual turning in addition to a manual Bridgeport mill as well as the CNC mill that was supplied three years ago by Braithwaite Machine Tools as a high-class rebuild complete with two-axis MillPWR.
"I've always found MillPWR so easy to use," comments director Mark Youngman. "Even though it was my first CNC mill, I was up and running within a day. I simply transfer DXF files from computer, and I would best describe the control as a programmable digital readout.
"But with the two-axis CNC I soon found that I was continually interrupting other jobs to go back to the mill to manually bring the quill down for successive cuts."
The answer, of course, was to upgrade to a three-axis CNC and, in Mark Youngman's view, "there was no question of considering a different control system because MillPWR cannot be made any simpler".
Targeted at intuitive knee milling applications, the user-friendly MillPWR supplied by ACI (UK) is designed to speed machine set-ups and minimise scrap while producing consistently accurate and repeatable workpieces via a host of standard features and easy-editing routines:
- Explode – explode a program step into several, more detailed steps for easier editing;
- Reverse step – switch the start/end points and tool offset of any step;
- Reverse path – reverse a continuous tool path;
- Change steps – change/edit the depth, offset and feed rate of several steps simultaneously;
- Delete steps – erase single or multiple steps; and
- Copy/move steps – duplicate or re-arrange steps.
MillPWR allows the machine to operate in either manual or CNC mode, even to switch between modes in the same program, and boasts a long list of special functions – for skew, rotate, mirror image, contour, engrave, ellipses, chamfer, island and spirals, for example – as well as an electronic edge finding capability.
The next step is for Mark Youngman to link MillPWR with a three-dimensional CAD/CAM system, to create an integrated solution to contour machining via the ability to combine G code machining files with conversational programming routines.
SOURCE: ACI (UK) Ltd,