CIMdata Reviews Virtual Gibbs Software
By Alan Christman, VP, CIMdata Inc
A major software release of Virtual Gibbs from Gibbs & Associates software is produced typically on a 9-month basis. Version 5.0 is evaluated here. Given the modest price of the software and the functionality provided, Virtual Gibbs offers good value to users.
Growth of Virtual Gibbs software can be attributed to its ease of learning and use, an internally developed integrated product line, strength in basic milling and turning, technology leadership in targeted areas, moderate pricing, establishing defensible market niches, an extensive dealer network, and a knowledgeable and astute management team.
A common user interface across all applications, continuous prompting, context-sensitive help, free-form programming to execute changes at any time, a flat menu structure, and a Windows-compliant interface—all contribute to the intuitive nature of the product.
Virtual Gibbs is most competitive in general-purpose machine shops that have a wide range of requirements and that value simplicity, programmer productivity, and modest software cost. It is also being effectively used in production machine shops with strong needs for turning, drilling, and 2 ½-axis milling. Virtual Gibbs is competitive, but less appropriate for mold, tool, and die shops that are focused on multi-surface machining of complex objects.
Solid-based machining
However, in some of these shops the solids-based machining capability provided in Virtual Gibbs could be of significant benefit. Virtual Gibbs is written with Microsoft development tools, operates under Windows 95, 98, and NT, and has a Windows-compliant user interface. It includes internally developed products for geometry creation, production milling, advanced milling, production turning, toolpath verification, and post processing.
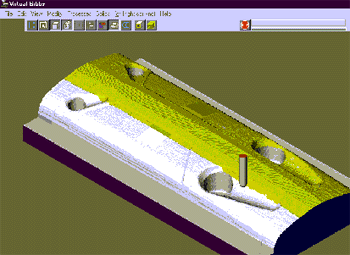
Gibbs' SolidSurfacer provides integrated manufacturing modeling and machining of solid and surface models. With SolidSurfacer, which is built on a Unigraphics Solutions Parasolid base, users can create, import, modify, and machine solid and NURBS-based surface models. Solids and surfaces are treated as bodies and sheets. They can be intermingled within an object and users can operate in either a surface or solid mode. In addition, Gibbs has extended its offering by developing a feature recognition capability.
The Gibbs method of providing solid modeling and solids-based machining is relatively unique. As opposed to embedding its CAM software within an industry-accepted third-party modeling product, Gibbs has licensed both the Parasolid and ACIS kernels. As such, Gibbs is not dependent on a single CAD supplier. The software offers an open environment for direct receipt, without translation, of all CAD files based on these kernels. Further, since Gibbs does not resell a third-party modeler, potential sales conflicts with resellers of CAD modelers are eliminated. CIMdata believes there is considerable merit in the Gibbs approach.
Programming automation
Gibbs continues to focus on enhancing programming automation. It was one of the first CAM-centric vendors to provide programming associativity. As such, toolpaths can be quickly regenerated as changes in geometry, tooling, or machining parameters are introduced. Further, the "process" command on the main menu permits an adaptive approach to knowledge-based machining. Users can store a full machining process and then retrieve and re-apply this process to a similar situation. The process can be used directly or adapted to the new circumstance. Knowledge-based machining rules are included throughout the software.
CIMdata believes that Gibbs provides industry-leading product capability in 2- and 2 ½-axis operations. This has been the traditional strength of Virtual Gibbs. With the introduction of SolidSurfacer, Gibbs has also become competitive in 3-axis multi-surface milling and machining of solid models. Gibbs does not support simultaneous 5-axis milling, wire EDM, 4-axis turning, or sheet metal operations. Lack of these functions can be significant deficiencies in some environments.
Gibbs is a leader in bringing programming to the shopfloor. The company is one of the few vendors to offer its current production software to the controller market. A number of major controller manufacturers and machine builders now include Virtual Gibbs SFP v 5.1 (See "Leading CNC Builders Will Begin Shipping Gibbs V5.1") within their controllers. This permits users to implement identical software for both off-line and on-line programming. This relatively unique approach increases the pervasiveness of Virtual Gibbs among users and provides for incremental revenue to the company.
Basic machining
The Virtual Gibbs basic machining products are Production Mill, Advanced Mill, and Production Lathe. Production Mill supports 2 ½-axis and single surface 3-axis machining of wireframe geometry. Basic modeling, IGES support, and a single post-processor are included in the standard Production Mill package. An Advanced Mill option provides multiple coordinate systems to define geometry in non-XY planes, fourth and fifth axis rotary positioning and support for tombstone machining. Also SolidSurfacer CAM can be employed to provide 2 ½-axis machining of solid components.
Gibbs does not provide a standard tool or material library. Instead, it offers the industry accepted Cutdata machining libraries from IAMS as an optional third-party product. Cutdata includes a cutting tool library, material library, and a machining technology library. The tool library includes information on toolholders as well as cutting tools.
Appropriate cutting information such as recommended feeds and spindle speeds is provided for various cutting tools and materials to be machined. The user can accept the default conditions or specify key parameters such as feedrate, spindle speed, depth of cut, location of safety plane etc. Some users elect to build their own tool and material libraries as opposed to acquiring the Cutdata library.
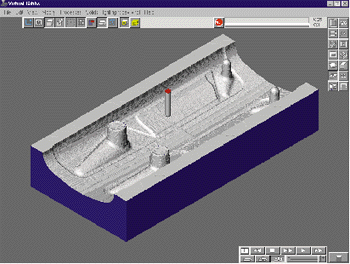
With a tool library, categories of available tools such as face mills, drills, taps etc can be graphically displayed. Supplementary information, such as dimensions or the number of flutes, can be added. Users can create their own tools. Once defined, new tools can be added to the library. A tool data management system with shopfloor control of tools is not provided in Virtual Gibbs.
Machining parameters are established within the Virtual Gibbs Operations Manager. The software suggests feeds and speeds as a function of the cutting tool being used and the stock material. The values can be overridden on a one-time basis or the recommendations can be replaced. For example, the system suggests a step-down or it can be manually entered. If parameter values are entered that are outside of the pre-determined acceptable range, the software will display a message to the user.
Production turning
Virtual Gibbs Production Turning is one of the industry-leading lathe packages. All basic turning functions are provided. The modeling capability is the same as that in Production Milling. Associativity between the geometry and the toolpath is provided. Toolholders and a total of 15 categories of tool inserts are in the tool library. Cutdata software is used to provide appropriate feeds and spindle speeds as a function of stock material and cutter being employed. The feedrate can be set such that cutting occurs at a constant surface feet per minute. Different feeds and speeds can be established for different boundaries on the part. Toolpaths can be defined so that the tool cuts in both directions or in one direction only.
In turning, unlike surface milling, the amount of material remaining is known to the system. As such, a re-machining operation is available to remove only the material left after a cut. Support of this function in turning is a relatively uncommon capability. Also, air cutting is avoided as tool moves are calculated to cut only in areas where material remains. Canned cycles are available. The full tool insert is considered in collision avoidance, but the toolholder is not considered. Production Milling and Turning are available in a single package.
Grooving and threading operations are supported. Bi-directional cutting is supported in grooving. Also, a drag capability in grooving is provided to minimize burrs.
A mill-turn option is provided. It allows users to perform rotary milling on lathes. This includes machining of slots, holes, cross-drilling, engraving, pocketing, face milling, and face drilling. Separate milling and turning products are used, but the output is combined into a single program.
In Virtual Gibbs the user has the option of independently generating a toolpath. In this case, the user picks a tool and then manually moves the tool over an area to generate a toolpath. However, toolpath computations cannot be saved, scheduled, and processed at a later time. This feature is important for complex tasks that necessitate long computation times, such as that encountered in mold and die machining, but is less important in a typical Gibbs environment.
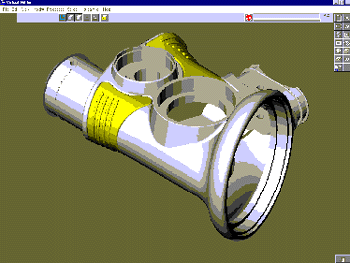
An information packet can be produced for the shopfloor. A typical packet includes an operation summary, a tool list, a copy of the NC program, machining times, and screen shots at each stage of machining. Interactive editing of toolpath is provided. An editing function can be useful to allow machinists on the shopfloor to make small corrections to a toolpath. It can also be employed to optimize a toolpath and thereby reduce machining time when producing production quantities of a given part.
Gibbs does not encourange software customization. The company does not provide a customization language or support embedding C language macros in the code. Gibbs does not support wire EDM machines or sheet metal operations. A specific mold base design product is not provided.
In Virtual Gibbs SolidSurfacer CAM, Gibbs offers users the option of machining complex shapes directly on a solid or a surface model. Machining of solid models typically produces better results than that from surface models, as the integrity of the model is guaranteed. When discontinuities, incomplete, or inadequate surface conditions are encountered, Gibbs recommends that users utilize or create a solid model and machine on the solid. However, since surface machining is usually faster than solid machining, cutting well-defined complex objects is usually done on a surface model. Having the capability to machine on either a surface or a solid provides a significant competitive advantage for Gibbs. Most Gibbs customers machine on a solid model.
Toolpath verification
Unlike most vendors who utilize a third-party product for toolpath verification, Gibbs has internally developed a verification product capability for each machining module. By so doing, Gibbs is able to offer integrated machining and verification. This permits the user to see a common interface across modeling, toolpath generation, and toolpath verification applications.
The Cut Part Rendering function provides industry-competitive toolpath simulation and verification. One can pick any toolpath or group any number of toolpaths for visualization. This is typically done after each operation. Visualization of the cutter can be turned on and off. Tool movement can be slowed, backed up, paused, or the view can be changed during animation. The operator can control the simulation speed. Layers of cuts and sections through the part can be shown. Both feed and rapid moves are shown. The solid model can be sliced to examine details at a specific location.
Virtual Gibbs presents a solid representation of the cutting tool and the part model, as opposed to a faceted surface. The actual shape of the tool is depicted as opposed to using one or more cylinders to display the tool. Verification is not performed until the complete toolpath is computed, as compared to concurrent toolpath computation and display. Verification is performed on the CL file, as opposed to the posted file that will be read by the machine tool controller.
Gibbs believes that post-processing is a strategic component of its business. As such, Gibbs offers a turnkey solution for its customers, which includes the necessary post-processors. Gibbs maintains a library of about 2500 posts. From this library, internal Gibbs personnel or resellers modify and develop the necessary posts for each customer. An unconditional factory guarantee is provided to the user. Gibbs provides the support to correct any problems that occur. The post generator used by Gibbs is available for purchase by more experienced users. All of the Gibbs posts, which are specific to the Virtual system, are continually upgraded as the Virtual software is enhanced. This is not common in the industry, as most vendors only upgrade posts as required.
This is one in a series of NC software reviews by CIMdata Inc. A complete detailed review may be purchased from CIMdata Inc, 3909 Research Park Drive, Ann Arbor, MI 48108; phone: 313-668-9922
Gibbs and Associates Inc, 323 Science Drive, Moorpark, CA 93021; phone: 805-523-0004