Crankshaft Manufacturer Adopts Flexible Machining Line
Wing-type CNC modules offer programmability with volume production.
Atlas Inc (Fostoria, OH), a division of Cummins Engine, produces crankshafts for the company's heavy-duty diesel engines. To improve fuel economy and power for its truck customers, Cummins has developed a new 600-hp, 15-liter engine to eventually replace a heavier 14-liter engine.
The challenge facing Atlas' manufacturing engineers: to reconfigure and retool their plants to meet product changes aimed at evolving market needs. Challenges included engineering changes common to new product launches and the capability to produce in volumes matching market demand.
Atlas called on Tuff Machine (Warren, MI) a machining system integrator, designer, and builder, to help develop the best manufacturing response. Tuff's assignment was to develop a process for milling a notch in a counterweight of the 15-liter crankshaft, a tough-to-machine microalloy forging, drill a dowel hole, and drill and tap 12 end holes—all in a 3-minute cycle. The production machine also had to have the reprogrammability of CNC.
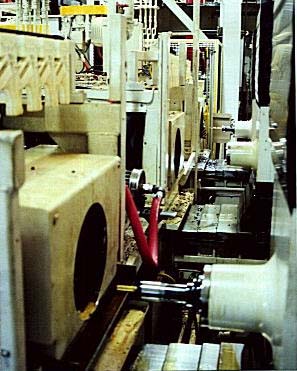
Selecting from the best options
As a machining system integrator, Tuff Machine develops a complete process including drilling, milling, tapping, and material handling for its customers. It can choose virtually any component to build into its systems. For its typical customers—automotive component producers—Tuff frequently specifies the 15-hp CNC wing unit from Cellular Concepts (Detroit, MI) for its cost-effectiveness and application flexibility, according to Dale Naturkas, Tuff VP.
"Properly processed and integrated into a system, the Cell Con CNC module has often proved to be a super unit," says Naturkas. "It provides superior metalcutting value for the dollar. We have been integrating the Cell Cons for more than 10 years and use one ourselves."
"We saw the Atlas application as ideal for the CNC Cell Con wing unit," he adds. At Atlas the reprogrammability of the CNC—not only for part changes but also for compensating moves to make the product correctly—was a key feature, Naturkas points out.
"In addition, the low profile, large work envelope, and small footprint ft this application like a glove. A standard JIC mount and the wing base design made it easy to apply to the other elements in the system, such as the walking beam transfer. And the independent CNC unit is simple to integrate into our system and to manage once it is part of a system," says Naturkas.
The customer's point of view
"The biggest reason we went with CNC wing units is for flexibility, without a doubt," explains Steve Allgyre, Atlas senior process engineer. "The CNC makes it simple to accurately adjust for changes in feature locations on the part—simply reprogram rather than shimming as we would have to do on a dedicated piece of equipment. We have already made many adjustments since the installation, and we are ramping up production to more than 50 cranks per day for the short term, and possibly several hundred a day, longer term."
In operation, a walking beam transfers cranks into the first station of the machine. At this point, a Cell Con module drills a bolt hole circle in the end of the part at 14 ipm drilling speed with coolant-through carbide tools. At the opposite end, another Cell Con module drills the dowel hole. Tapping is tough. The forged material is difficult-to-machine microalloy with chromium, magnesium and other elements that produce stringy chips all through the machining process.
In the second machining station, a notch is milled into a counterweight in the middle of the shaft. Opposite this milling station is a spare Cell Con, installed at that point for two reasons: as a backup in case a Cell Con goes down or is out for rebuilding. All that is required is a quick tool change and reprogramming for tapping or drilling or to accommodate possible future part variations or changes—changes within the product or to an altogether different product. The CNC provides complete process flexibility.
Easy to choose CNC modules
"I could potentially mount three additional Cell Cons opposite the ones installed here today," Allgyre says, "and perform any variety of operations that may be required by a new part design or change. And the cost to do so would be very economical."
Tuff finds that customers are, more than ever, looking for the flexibility to handle a variety of parts, maintainability, and minimum floor space.
"When you mention CNC no one complains—even in a high production shop," Tuff's Naturkas says. "They understand that for future product changes, CNC allows them to make the change—within the limits of the work envelope. The only thing we have to watch is the cycle time compared to previous dedicated machining stations. A dedicated station can drill six holes at once, where a CNC unit drills one hole six times. But the latest CNCs are fairly quick and are becoming faster."
According to Atlas' Allgyre: "It was not difficult to persuade management to invest in the CNC route. It may have brought our manufacturing 20 years ahead compared to another system running about 250 parts per day, gang-drilling the part. It was fast enough, but it could only do one thing for its lifetime. And the life of dedicated equipment can be too short given the frequency of product and design changes we see."
Adds Tuff's Naturkas: "Our customers are finding that CNC makes it possible for them to retool our machines, or pull them off the line and make it a stand-alone for rework or other assignments. It is not a throwaway piece of equipment. It can be reused over and over, even if it comes out of the existing system. In this way, our customers are on the leading edge of the trend to reconfigurable systems," Naturkas says.
Cellular Concepts Company, 20580 Hoover Road, Detroit, MI 48205-1064; phone: 313-371-4800