Gilman Dovetail Slides Put Precision, Comfort into Contact Lens Manufacturing
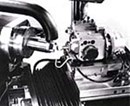
A small piece of plastic, a polymer actually, resting on the cornea of the eye, helps millions of people see better, comfortably. Contacts are precision-crafted lenses that improve vision and allow the eye to breathe normally.
Making the precision-crafted contact lens is a challenge that DAC Vision (Carpinteria, CA) tackles with two-, three-, and four-axis CNC lathes including the Series III/4XC four-axis lathe.
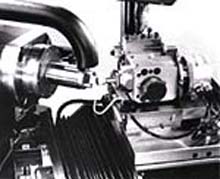
The 4XC four-axis, ultra-precision diamond turning lathe uses a left hand diamond tool (#1) to remove the majority of the material that is blocked or held directly by the collet and to form the contour. The final cut is done with tool #2.
The 4XC lathe is fitted with the contact lens software package offering edge radius input and producing reliable and repeatable radii on spherical and aspherical designs. The machining time is typically less than 60 seconds per side.
Since the ultimate goal is contact lens comfort (which depends on shape, lift, and thickness of the lens edge) and precision, the 4XC is vital to the comfort of contact lens wearers. According to DAC Vision, "Performance is not just nice surfaces—our customers' eye care professionals must be able to improve their patients' vision."
DAC Vision utilizes Gilman DC6, DC8, and DC10 (6, 8 and 10 in. widths) cast iron dovetail slides in its lathes to ensure absolution accuracy, stability, and ultra-smooth, vibration-free motion. These are fitted with leadscrews, bearings, plates, and accordion way covers.
"In our applications it is critical that mechanical resonance and electrical noises do not find their way to the lens surface. Gilman cast iron dovetail slides really do the job." Gilman slides are used as a positioning stage by adding brushless motors, rotary and linear encoders and cabling to the computer numerical control. This combination allows the slide to have 0.1&3181;m resolution from the linear encoder to ensure absolute positioning, and 0.050 µm resolution from the rotary encoder to synthesize the tachometer and provide the best possible resolution during the cut cycle.
Russell T. Gilman, an SKF Company, is an ISO 9001-registered global supplier of high precision machine components, including slides, spindles, customized modular components, and index tables.
Russell T. Gilman Inc, 1230 Cheyenne Ave, P.O. Box 5, Grafton, WI 53024; phone: 414-377-2434