Gleason Puts Power of CNC Machines into Dry Gear Cutting
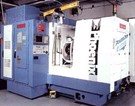
Carbide improvements are critical.
Founded in 1865, Gleason Corporation (Rochester, NY) has long been a global leader in the technology required to manufacture precision gears for the automotive, aerospace and aircraft, truck, recreational vehicle, and power equipment industries. Gears produced by Gleason's machines are used in drivetrains for automobiles, sport utility vehicles, trucks, buses, as well as aircraft and marine, agricultural, and construction machinery.
Gleason's products and services include machinery and related equipment for the production, finishing and testing of gears. A worldwide support system provides tooling replacement parts, field application service application development, gear design and inspection software, training programs, engineering support, and machine rebuild and upgrade services. Gleason also provides the technologies required for producing prototype and production gears.
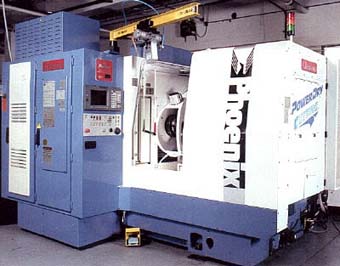
Improvements in carbide grades and sintering processes in combination with new coating methods and the use of CNC machines have led to a significant new trend in the way cylindrical gears are produced. This trend combines high-speed hobbing using coated carbide tools—without coolant. Provided that process parameters are set optimally, extremely short cutting times can be achieved with long tool life and high part accuracy. Process development in bevel gear cutting also benefits from the carbide and coating developments.
Carbide tools improved
Gleason calls its most recent breakthrough in technology—Power Dry Cutting technology. Two important developments have led to this development. Though high-speed machining using carbide has been known for some decades for milling and turning operations, the intermittent character of the gear cutting process had delayed the use of carbide tools in gear manufacturing. Carbide was found at first to be too brittle for interrupted cutting actions. Subsequently, a number of different carbide grades were developed. Though the first successful studies in carbide hobbing of cylindrical gears were completed in the mid 80's, it still did not lead to a breakthrough in the use of carbide cutting tools for gear production. Since the carbide was quite expensive and the tool life was too short, a TiN-coated high-speed steel hob was more economical than an uncoated carbide hob.
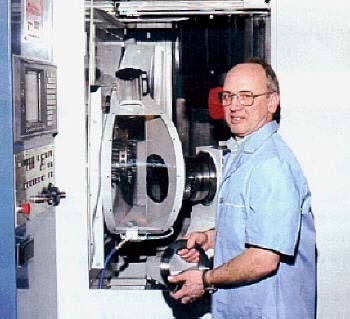
It is now known that the coating is a key factor in the use of carbide tools. The coating lowers the friction between the chip and blade front face and protects the porous surface of the carbide. Heat and friction cause chemical reactions between the chip and the carbide binder material and "washes out" the carbide grains on the cutting front face, causing a cratering wear pattern. The combination of fine grain carbide with the well known TiN coating is sufficient for skiving operations and leads to reasonable tool life
Cost comparison: Carbide vs. HSS
The higher cost of carbide for the cutting tools is not really a limiting factor. Gleason's analysis includes the following cost comparison of the Power Dry Cutting based economic viability when compared with conventional High Speed Steel (HSS) for the cutting tools:
Cost of carbide blade sticks (five times price of HSS)
Sharpening of carbide blades (about twice the time of HSS)
Coating of carbide blades (only once necessary for HSS)
Building of blades in cutter-head (twice the time of HSS)
Tool life of carbide (1.5 to 3 times of HSS)
Manufacturing time = machine occupation (20 to 30% that of HSS)
Gleason concludes that the cost of the carbide and the coating is more than compensated by fewer numbers of resharpenings, requalifications and so forth. In this example, the total tool cost per manufactured gear is reduced by 28%.
High-speed spindles a key
Applying the Power Dry Cutting method requires Gleason Phoenix bevel gear generators equipped with special high-speed spindles. Conventional machines with the traditional cradle design cannot handle cutter spindle speeds up to 800 rpm. The complicated geartrain in a conventional machine cannot produce smooth, coordinated motions and maintain stable temperatures at high cutting speeds.
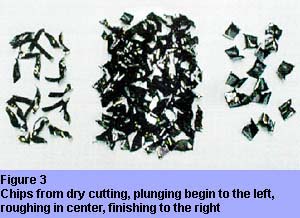
The six-axis, free-form Phoenix machine, however, has the cutting spindle motor mounted directly to the same vertical slide that houses the cutter spindle. The design uses no complex couplings or mechanisms to transmit power to a tilted cutter-head, as on cradle style machines. Power Dry Cutting can be applied to single index face milling or continuous index face hobbing and is always a completing operation.
To set up the machine for dry cutting, Gleason has developed a chip-guiding channel that takes advantage of the kinetic energy and the aerodynamic shape of the chips. The chips fly tangential to the cutter in the direction of the back guarding, where they fall into a Venturi system that transports them to a cyclone without the need for either an auger or chip conveyer. Except for two pressure air nozzles, no energy is applied to remove the chips and maintain a perfectly clean machine interior. Up to 80% of process heat is removed from the machine together with the chips, with no heat transfer to the machine elements.
An environmental plus
In the dry cutting configuration, the Phoenix machine has no oil tank, no chiller unit for cutting oil, and no chip conveyor. This results in a 30% reduced floor space and a very compact appearance of the machine tool. In the Phoenix 450HC, the chip channel is visible in the center, surrounding the complete work area of cutter head and workpiece. The front part of the channel can easily swing aside and allows a convenient change of the cutter head.

Power Dry Cutting has significant advantages with regard to the industrial environment compared with conventional bevel gear and pinion cutting. Because cutting is not used, the machine interior and surroundings remain clean and dry. Safety during changeover and while operating the machine is higher. Operators (and their skin) don't come into direct contact with cutting oil or breathe oil mist. Health risks such as sore throats and skin rashes are virtually eliminated in a dry machining workshop. Workpieces leave the machine clean and dry; chips are not contaminated with oil, eliminating the need for costly separation or disposal of the cutting oil from the chips. In fact, the cost of cutting oil, logistics, and storage expense are all eliminated.
The Gleason Works, 1000 University Ave, Rochester, NY 146-92-2970; phone: 716-473-1000