Laser-Based Powder Metal Process Builds Up Rapid Prototypes
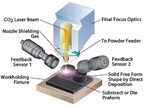
Precision Optical Manufacturing (POM: Plymouth, MI) has introduced its Direct Metal Prototype technique for producing fully dense metal prototypes from tool steels, aluminum, copper, and other metallic materialsdirectly from a solid model CAD design. The DMP (a trademark of POM) process enables users to produce fully functional, 100% dense, near-net shape parts. In addition, the DMP technique provides the ability to embed objects in the prototypes, such as sensors, copper heat sinks, thermal barrier, ceramic matrices, and/or internal passages. The DMP process was introduced at the Rapid Prototyping & Manufacturing Expo in Chicago.
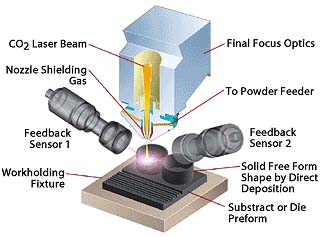
DMP parts are manufactured used POM's Direct Metal Deposition (DMD, a trademark of POM) process technology, a micro-casting technique that builds up metal layer by layer. DMD is an additive process that takes moldmaking and metalworking in an entirely new direction, producing improved material properties in less time and at lower cost that is possible with traditional fabrication technologies.
DMD's laser-based powder metal fabrication process provides a "near-net" shape part, fully dense metal mold or die cavity directly from a solid model CAD design," explains Dwight M. Morgan, president & COO. The DMD process can also be used to salvage and repair cracked, broken, eroded, or heat-checked surfaces. Damaged surface can be replaced with tool steel alloys or custom POM alloy compositions, tailored to specific applications, Morgan points out.
How the DMD process works
The DMD technology is the result of blending five common technologies: laser, CAD, CAM, sensors, and powder metallurgy. The resulting process creates a metal prototype part by focusing an industrial laser beam on to a metallic workpiece or preformed part, creating a molten pool of metal. A stream of metallic powder is then injected into the metal pool, increasing the size of the molten pool. By moving the laser back and forth under CNC control, tracing out a pattern defined by the CAD geometry, the prototype part is builtline by line, one layer at a time.
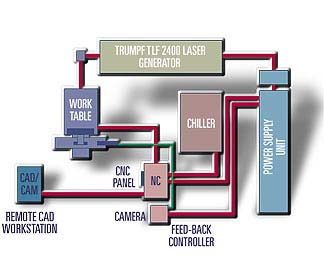
The molten pool solidifies at a rapid rate, resulting in a fully dense, refined microstructure. Prototype parts fabricated by the DMD and DMP technique have physical properties that exceed those of conventional wrought or cast materials and are said to provide superior quality and increased strength. More important, with this technology, the metallic composition can be altered "on the fly" by injecting different types of metal powders into the melt pool, providing the possibility of fabricating composite hybrid material metallic parts. POM's e-manufacturing (a trademark of POM) software optimizes process efficiency, compressing production time and reducing cost.
Precision Optical Manufacturing Co Inc, 44696 Helm Street, Plymouth, MI 48170; phone: 734-414-7900