Laser Brightens Productivity Picture at Lighting Reflector Company
With a backlog of stamping trim and form dies waiting to be produced for custom light reflectors, and customers demanding 24-hour turnaround, Reflek Corp (Fall River, MA) knew it had to do something totally different.
According to Gary Bienvenue, CNC department manager, and Reflek salesman Robert Dorsky, a way had to be found to dramatically reduce the time and investment in hard tooling costs to make slots, holes, windows, and flange shapes in the thousands of light reflectors the company produces every year.
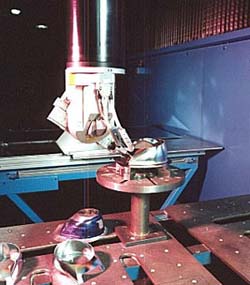
Normal turnaround for stamping press trim dies takes from eight to twenty weeks and customers often make last minute changes, which requires tooling changes. Besides, some customer demanded leadtimes of 24 hours for prototype reflectors.
Finding a better solution
Most reflectors that Reflek produces are used in commercial buildings. Some, however, find their way into residential housing primarily in recessed lighting fixtures. Two methods are used to form the deeply cupped reflectorsspinning and hydroforming. Both methods require a die that the metal, usually thin gage aluminum, is molded to. A reflector starts off as a flat metal blank stamped from a coil. In spinning, the blank is mounted in a lathe-style CNC machine, spun and shaped over the die with an arbor that uses a rotating disk. The disk contacts the metal and forces it over the die.
In hydroforming, pressurized hydraulic oil is used to force the flat aluminum blank over a die. Once the reflector is formed, it still needs final finishing and holes, slots, or windows cut into it for the light source and wiring.
Aluminum is the primary metal used for reflectors with a small percentage made of steel and brass. Thickness of the metals varies from 0.025 in. to 0.080 in. The company's production quantities can range from 10 to 25,000 reflectors with an average of about 500 to 1000. The smallest light reflector produced was 1 ½ in. in diameter with the largest measuring 4 in. for the medical industry. Work is done with two 10-hour shifts, five days a week, with 10 hours on Saturday.
Lasers shine bright
Reflek turned to laser technology for the answer, specifically a Rapido 5 Laser Processing Center from Prima U.S. Inc (Farmington Hills, MI) to meet its backlog (which stood at record levels) and customer demand for faster turnaround.
Trim dies that did what the laser now does are expensive to produce and require a long leadtime. For some parts, the trim dies must match the complex shape of the reflector to cut an accurate window in it. These complex dies require excessive machining time because the die needs to be made with a ball nose milling cutter taking light cuts to get the proper shape to match the die. In addition, the costs of the trim and hole die include CNC machine time, skilled technician labor, programming time, machine fixturing, expensive tool steel used to make the die, and outside heat treating and handling.
A versatile laser machine
The Prima Rapido 5 eliminates all of this except the programming time. Eventually all programming will be done off-line to extend the laser's uptime for producing parts rather than taking time to program on the machine. Reflectors can take from ten minutes to a half hour to program on the laser, depending on the complexity, using the machine's teach pendant.
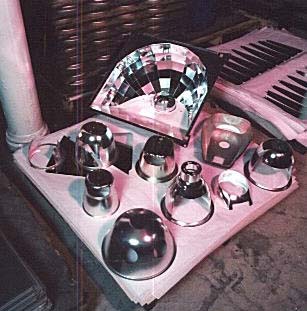
Overall tolerances of ±0.005 in. and hole tolerances of ±0.002 in. are easily held by the Rapido 5. Gary Bienveue has designed his own universal-style jig fixtures for fast setup on the machine's bed. However, on some jobs, precise jigs were made because of the need for extremely accurate repeatability.
Prima's Rapido 5 can be equipped with CO2 lasers from 2200 to 6000 watts of laser power for cutting, welding, and heat treating applications. The unit has seven quick-change laser heads that offer metalforming and fabricating operations the ability to perform a broad range of cutting, welding, heat treating, and cladding applications, all on one five-axis laser machine.
The quick-change cutting heads allow an operator to change laser heads within 60 seconds. Lenses are pre-centered so no alignment or calibration is necessary. All cutting heads are equipped with Prima's Safe Impact Protection System (SIPS), which prevents damage to the head in case of interferences and allows for quick recoupling of the laser head attachments.
Prima U.S. Inc, 23399 Commerce Drive Suite B-10, Farmington Hills, MI 48335; phone: 248-442-4994