Case Study: Machine Speed Increased By 20% With DURAFLEX Cups
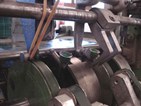
Introduction
Bertex Mail AB is a print finisher, located in Helsingborg, Sweden. As a major player in the graphic industry, the company needs to maintain high speeds and productivity on an hourly basis. Recently, Bertex strengthened its production line with an adaptation to its Muller Martini feeding machine.
Problem
As abrasive and sharp paper materials ran through the feeding machine, the lip of Bertex's vacuum suction cups were being destroyed every few hours. The tearing and cutting of the suction cups resulted in the company having to change two cups four times each day. Not only was the cost of replacement suction cups rising, there was also an increase in production downtime caused by the swapping out of destroyed cups.
Solution
Bertex decided to work with its vacuum partner PIAB to address the situation. The company had been utilizing PIAB's vacuum pumps for over a decade, and wanted to find out if its suction cups would stand in a test of durability.
"We installed two new suction cups, fitted directly onto the machine's standard suction cup holder. No adaptations or changes were needed; it was an incredibly easy installation process," said Mikael Ravn.
The model BX25P suction cups fitted onto the Muller Martini machine are part of PIAB's DURAFLEX™ line. These suction cups are made of a revolutionary polyurethane material that combines the soft elasticity of rubber with the exceptional wear-resistance of polyurethane. Unlike conventional suction cups, which often cause micro-leakage, the unique DURAFLEX material allows PIAB's cups to form a proper seal on the material being handled. These attributes made them the ideal solution for Bertex's difficult application.
Result
The result of the change in suction cups was enormous savings for Bertex. "We are now spending 95% less on suction cups. Instead of going through eight suction cups each day, we now to through only six each year."
Not only is the company saving a great deal of money on the actual suction cups, they have also been able to run the machine 20% faster since the PIAB suction cups have a larger area. This means the gripping force is higher, allowing production to increase from 10,000 to 12,000 sheets per hour. In fact, the top speed to the machine can now accommodate 16,000 sheets per hour.
Because the cups are replaced much less often, and can be fitted directly onto the machine, downtime has also been greatly reduced. Bertex can now operate at higher speeds with more reliability and productivity.
SOURCE: PIAB