New, High-Speed Measuring Machine For Flat Components
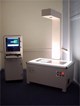
Companies in the UK involved with the manufacture of flat components using power presses, laser or plasma profiling machines, turret punch presses, water jet cutting machines or routers may inspect their components on a purpose-designed measuring machine from Press & Shear Machinery, Tamworth, newly appointed agent for the manufacturer, InspecVision, Northern Ireland.
Called Planar, the machine is unlike other systems on the market in that it has no moving parts, allowing it to be sold at an extremely competitive price. Amortisation periods of less than two years are easily achievable.
Absence of moving parts also avoids wear and the need to recalibrate the machine periodically. It is almost impervious to vibrations and can be installed on the shop floor, even adjacent to a punching machine. Manufacturers may therefore carry out first article inspection in seconds, reducing scrap and downtime. As the system measures a component in less than one eighth of a second, it can be integrated into a high-speed, automated production line, if required.
Available in five models with table sizes from 2.85 m2 to 0.35 m2, the Planar machine is designed to measure automatically the dimensional accuracy of any flat opaque materials, not only sheet metal but also paper, wood, plastic, cloth, cork etc. Accuracies ranges from ± 0.025 to ± 0.1 mm. The measurements obtained can be used to compare the dimensional accuracy of a manufactured component against its drawing or CAD model, or to reverse-engineer an existing part.
Another useful feature is the ability to digitise a printed drawing in seconds by converting it automatically into a DXF file, enabling the part to be manufactured on a CNC machine. The system even includes optical character recognition (OCR) and neural networks to extract text and dimension layers from the drawing. To create an accurate DXF manually can take hours, or even days.
All Planar machine are capable of measuring the thickness or flatness of a component using laser triangulation to measure the deviation of a spot point. This allows the height of any part of the object to be measured, including those places where gauges and callipers cannot reach.
The Planar system is resistant to scratches and dirt on the glass measurement table and can continue to operate if the surface is cracked. As ordinary glass and fluorescent lights are used, it costs only a few hundred Euros to get the system up and running again even if a component is dropped right through the table.
SOURCE: Press & Shear Machinery Ltd.