Non-Round Parts Can Be Turned on Any Good CNC Lathe
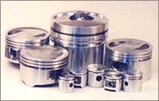
The self-contained camless system is accurate to within a few microns.
A new high-speed solid state actuator is at the heart of new CNC shape-turning system called Pulse-Turn that can turn piston skirts and other non-round parts several times faster than current conventional technology. Though developed for machining pistons, the technology has shown great promise and is being evaluated for such diverse applications as turning hydrostatic bearings and jet engine housings.
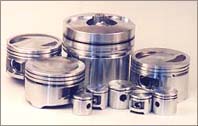
The Pulse-Turn camless system is fully programmable and accurate to within a few microns while turning pistons and other complicated shapes at speeds to 6000 rpm. For piston turning, the Pulse-Turn Model 25 controller can be programmed to generate single-, double-, and triple-ovality; variable ovality; and profile forms.
Pulse-Turn is a self-contained accessory that mounts on "suitable" standard CNC lathes and consists of a toolholder/actuator carrying the cutting tool, an amplifier, and a controller. The critical point about the suitability of the CNC lathe is that it must be a good quality, accurate machine, whether vintage or brand new. The only interface to the CNC lathe required is a connection to a suitable spindle position encoder.
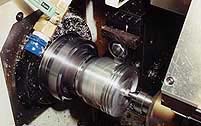
Mechanical operation of the Pulse-Turn contrasts significantly with current conventional machining methods for turning pistons. Most oval-skirted pistons are turned with cam-operated lathes or with specialized lathes using servo systems. Both control technologies provide large tool travels at relatively slow speeds. When the goal is performing short travels at speeds of several thousand cycles per minute—particularly when high accuracy is required—their large dynamic masses present insurmountable obstacles.
The Pulse-Turn actuator is a rod made of a "smart material"—so-called because it has the ability to change its physical shape when subjected to an external stimulus. In this case, the stimulus is a variable, programmable magnetic field and the phenomenon is known as magnetostriction. The material, which was developed at the Naval Ordnance Laboratory in search of a better sonar transducer, generates a thrust force of 600 lb and consequently has a high acceleration.
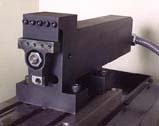
In the turning application, it produces a strain of as much as 1500 parts per million, i.e. a 10 in. long rod can expand .015 in. from its rest condition. Because the action occurs at the molecular level, the amount of motion can be extremely small and very repeatable. Its response is practically instantaneous and its performance doesn't deteriorate with time.
The toolholder/actuator has very few parts, no stick-slip, and no sliding surfaces. The actuator rod pushes a linkage that operates the toolholder, which is suspended by a flexing link. The total moving mass has been limited to less than 2 lb. Pulse-Turn develops a thrust force of 2670 N (600 lb) maximum, and has positioning accuracy of ±1.1µm (0.000 044 in.) and 1% of actual stroke. Positioning repeatability is 2.2µm (0.000 088). Actuator size is 70x130x460 mm (6.7x5.15x18.2 in.) and weight is 22 kg (48.4 lb).
The Pulse-Turn Model 25 controller includes a Windows-based user interface, a high speed DSP, and an amplifier.
Active Technologies Inc, P.O. Box 1691, Morristown, NY 07962-1691; phone: 973-889-9426