Okuma Demonstrates Taper-Turning On A Machining Center
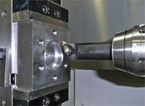
UK - At EMO 2007, the Japanese machine tool manufacturer, Okuma, introduced a new way of turning tapered bores and outside diameters using its horizontal machining centers, which are available in the UK through NCMT.
Called turn-cutting, the patented technique is in contrast to the established process of revolving a component on the rotary table of a 4- or 5-axis machining center and feeding in a static turning tool mounted in the spindle to machine the OD. The bore would be impossible to turn to any reasonable accuracy, as a long right-angle head would be needed.
Instead, the turn-cut function in the Okuma OSP-P200M control allows a single-point turning tool in the spindle of one of the manufacturer's horizontal machining centers to turn a static component, even on a 3-axis machine. It is achieved by taking advantage of linear feed rates up to 60 m/min to circular-interpolate the X and Y axes rapidly while feeding forward in Z.
The clever part, which forms the core of the patent, is the ability of the control to continuously orientate the tool in the spindle by rotating it at precisely the same speed as, and in synchrony with, the circular X/Y path. The tool therefore cuts at the correct rake angle at every point throughout the 360-degrees to ensure efficient and precise metal removal.
Cylindrical bores and ODs are easily achieved by keeping the X/Y travels constant, while tapers and other profiles can be turned by varying the amplitude of circular interpolation.
The benefit of turning on a machining center is that components can be finished in a single clamping, avoiding a subsequent set-up on a lathe and the consequent handling costs, increased floor-to-floor time and tolerance build-up. If parts are heavy and / or have eccentric bores or ODs, rotating them for conventional turning becomes difficult, requires expensive lathes and can lead to further inaccuracies.
At EMO, the machining center demonstrating the turn-cutting technique was an Okuma MA-600HB, which can machine workpieces weighing up to 1.2 tonnes within a nominal one metre cube. Turn-cutting accuracy is to within microns and it is this degree of precision that is crucial; some machine manufacturers might be able to approximate the procedure, but only for open-tolerance work.
As with all the latest Okuma machine tools, the MA-600HB features the manufacturer's Thermo Friendly Concept. Symmetrical design and electronic compensation from sensors around the machine structure and spindle hold dimensional drift to below 10 microns, even if the ambient temperature changes by up to 8 degrees Centigrade. Repeatability is ± 1.5 microns.
While turn-cutting is applicable to any component, the company singles out large, multi-port valves as particularly suitable for being machined in this way. Not only can the bores and flange ODs be conveniently turned, but it is also possible to single-point cut an accurate scroll pattern on the flange faces for improved sealability.
SOURCE: Okuma