Sliding Headstock Makes Rotary Transfer Machining Ultra-Precise
Swiss-style turning of rotating bar is key on Hydromat HT series.
Contents:
Superior turned parts
Special design
A Hydromat at heart
Hydromat Incorporated, (St. Louis, MO) has added its Hydro-Turn sliding headstock innovation at the infeed station of its HT 32-12 CNC rotary transfer machine, permitting Swiss-type turning of the rotating bar stock prior to cutoff and clamping. The result is superior part concentricity, ultra-precise diameter control, and consistent surface finishes of workpieces. The HT 32-12 is the first of a series of ultra-precise Hydro-Turn (HT) rotary transfer machines, the company says.
The patent-pending Hydro-Turn design combines the best capabilities of both sliding headstock and rotary transfer machine technologies and provides an entirely new manufacturing solution for precision partmaking.
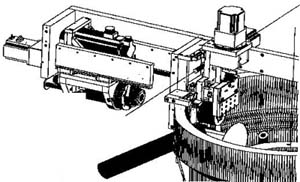
According to Martin Weber, Hydromat director of manufacturing, there is "a not-so-obvious but very significant advantage of combining a sliding headstock with the proven rigid clamping of a Hydromat rotary transfer machine." Users who previously bought ground bar stock to produce very precise parts can now buy less expensive drawn bar stock and there is no need to handle bar stock with special care or packaging, Weber says.
Back to top
With the ability to do Swiss-type turning at the infeed station, stock can be overturned for better OD dimensional and roundness control, eliminating the OD variability associated with cold drawn bar stock while also providing better roundness than ground bar stock, says Weber. "The benefit is that each part clamped subsequent to the first will have the same exact, precise OD tolerances, part after part after part."
Other advantages of incorporating Swiss-type turning at the infeed station include the ability to do additional operations in the lathe station—heavy recessing and turning and single-poinint—all before the part is cut off and clamped.
"This actually expands the capacity of the 12-station machine, offering more operations than previously possible, says Weber, "further reducing the need for secondary operations and opening up the potential for a wider variety of applications and more complicated parts."
Further, the rotating bar stock can be used to reduce cutoff time. Weber explains: "When we cut off a stationary part, we've got to cut off the whole part. With a rotating part, however we can cut two-thirds into the radius. Then we move the bar stock through the collet and into the first clamping station. Once it's clamped, we cut through the remaining material." Cutoff in two steps ensures precise alignment and takes less time.
Back to top
The HT 32-12 utilizes an entirely new casting design to accommodate the sliding headstock. An IEMCA Boss 542 bar feeding system, with a special telescopic nose for infeeding bar to the sliding headstock, is standard. Rotating bar stock is fed through a rotating collet to an air- and hydraulically-activated guide bushing. The stationary guide bushing rotates with the bar and is driven by a timing belt synchronized with the 5,000-rpm (maximum) air-cooled main spindle.
With a 32 mm capacity, the HT 32-12 is design to produce high-precision parts from standard bars up to 12 ft long. Spindle bore is 37 mm. Headstock stroke is 200 mm. Ballscrews drive the X, T, and Z axes. Rapid feedrates are 20 m/min (Z axis); 15 m/min (X axis); and 15 m/min (T axis). The main spindle is powered by 5 kW AC servomotor. X-, Z-, and T-axis drives are powered by 1.5 kW, 0.75 kW, and 0.75 kW AC servomotors, respectively.
The sliding headstock tooling package consists of quick-change gang tooling with four 19 mm (3/4 in.) toolholders—one to cut off the bar (which in some applications can be used to turn other features) and three additional tools for recessing, contouring, single pointing, and heavy turning.
Back to top
In addition to the sliding headstock design, the HT 32=12 is a modular system consisting of up to 12 horizontal and 6 vertical toolspindle units. Once cut off, the stationary workpiece undergoes many types of machining operations (drilling, cross drilling, boring, turning, milling, external and internal recessing, threading, tapping, broaching etc) The HT 32-12 has an inverting unit that removes the workpiece from the collet, turns it 180 deg, end-for-end, and places it precisely back in the same collet, which is being continuously flushed with filtered coolant. In this manner, the backside of the part is completely machining, thereby eliminating the need for secondary operations.
Hydromat Inc., 11600 Adie Road, St. Louis, MO USA; phone: 314-432-4644