Software Enhancements Make Walter Helitronic Tool Studio Even More Powerful
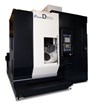
The series of enhancements made to the latest Version 1.9 of the Helitronic Tool Studio grinding software system now available from WALTER Machines UK of Honiley near Kenilworth not only offers additional features for tool regrinding and production, but they also allow users of Walter Helitronic multi-axis tool grinders to be even more efficient – and flexible – in production.
As well as providing for the integration of the machine loading systems, and accommodating an automated worktable, the 47-operation functionality of Helitronic Tool Studio 1.9 now also features six new operations including the production of K-Land on profiles and straight drill gash, as well as probing for facing, Integrated Measuring System (IMS) probing, wheel dressing and the facing and grinding of eccentric necks,
The new capability for the production of K-land on profiles allows users to grind a K-Land on ball nose cutters' corner radius and form steps with tangential intersection to OD – and to configure the appropriate probing and grinding moves on drills in segments.
As well as now enabling the facing and grinding of eccentric necks (as a cylindrical or eccentric move), Tool Studio 1.9 also now includes functionality for the production of a straight drill gash independent of a drill point clearance operation. This can be linked to point profile and the profile probing operation, and it complements new functionality for the probing of facing and IMS probing.
The new option for the Automated Worktable adds the capability of an additional CNC axis to Helitronic Power or Vision grinders – as a driven ‘upper table'. While this axis can be used as a positioning axis in conjunction with a fixed steady rest or tailstock support, for the production/regrinding of long tools, the axis can also be utilised as a feed axis for a travelling steady rest, to ensure support and rigidity along the tool.
All these developments add to the software's powerful Feedrate Optimiser and the Tool Balancer options functionality.
The Feedrate Optimiser capitalises on Tool Studio's intricate knowledge of grinding moves and wheel model as well as tool simulation to calculate instantaneous grinding wheel and machine spindle loads, to precisely set optimum feed rates and to manage wheel and machining loads.
At every point, the feed rates are set using user-specified wheel load and actual wheel load – low wheel load actions are therefore made faster and, importantly, moves that exceed desired wheel loads are slowed down.
The advantages here include increased productivity - in some cases, especially with complicated tools, time savings of 40 per cent or more are possible and grinding costs are therefore reduced – and extended wheel life.
Tool Studio's Tool Balancer functionality eliminates the headache often encountered when high-speed machining with asymmetric tools such as unequally indexed end mills.
The resulting unbalanced force can, for example, lead to chatter vibrations, gouging, loss of part accuracy and uneven tool wear plus, of course, excessive load on machine bearings. Balanced tools have longer life, produce better quality surfaces and reduce wear on their ‘parent' machines.
Tool Balancer analyses the mass of the tool directly from the program and applies an automatic balancing. The Helitronic operator chooses his own balancing strategy, for example lengthening the flute or deepening the core of selected teeth to perfectly balance the tool, without compromising the original cutting geometries – including unequal indexing/helix.
SOURCE: WALTER Machines UK Ltd.