Valenite's QC System Tackles Milling Cast Irons
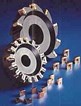
Valenite Inc.'s "QC System" of milling cutters, carbide grades, and positive top form geometry have been designed for milling gray, ductile, malleable, and compacted graphite cast irons. Two new complementary coated carbide grades have been developed:
SM838 carbide grade has been developed for maximum wear resistance at high speeds.
SM318 provides greater toughness on roughing applications.
The QC System features two face milling cutter styles—both have a 0 deg lead for square shoulder and limited clearance milling. The first style, VFQS90SE Series is a general purpose cutter that uses screw-held square inserts with eight (8) cutting edges. Negative pocket geometry in the milling cutter body enhances rigidity and strength, resulting in highly reliable performance—reportedly, even under difficult machining conditions.
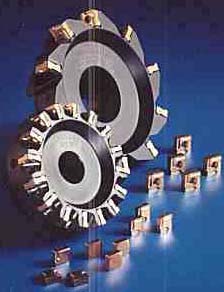
Milling cutter bodies styles range from an O.D. of 3 in. with five insets to a 12-in. diameter cutter with 18 inserts. Inserts use Torx lock screws applied with a maximum of 65 in./lb.
The second QC System face milling cutter body style, VFQF90SD Series features an adjustable design with wedge-held inserts. A special cam adjustment feature allows easy setup and highly accurate fine adjustment. By utilizing a fine pitch design, less frequent cutter indexes are required, maximizing productivity. Cutters range in size from 3-in. diameter with 12 inserts to a 12-in. diameter size with 48 inserts. Body styles are supplied with a hex wrench, wedge adjustment screw, insert wedge, and adjustment element.
Valenite developed and has applied for a patent on a positive top form geometry insert design specifically for use with the QC System. This new insert geometry reduces cutting force, provides freer chip removal, and extends tool life.
Two wiper inert designs are available for the VFQS90SD cutter series. These include a crown wiper and a top form wiper. The crown wiper has negative insert geometry and features eight (8) cutting edges. It can be used when the milling operation does not need to wipe a shoulder. The top form wiper has a positive insert geometry, which provides four (4) cutting edges. It permits wiping to a shoulder.
Valenite has also developed two new coated carbide grades to work specifically with the QC System. The new SM838 with titanium aluminum nitride (TiAlN) PVD coating has a very hard, smooth, and dense surface integrity. Combined with a substrate proven to have a good balance of wear resistance, toughness, and thermal crack resistance, it is well-suited for cast iron milling operations that perform at medium to high speeds (700-1200 sfm) and light to moderate feedrates (0.004-0.010 ipm).
The SM318 coated carbide grade is produced with the WidiaValenite multi-layer chemical vapor deposition (MLCVD) coating technology. SM318 uses 62 alternating UltraThin MLCVD layers of titanium nitride (TiN) and titanium carbonitride (TiCN). SM318 inserts resist microcrack propagation and can give more consistent tool life performance than competitive milling insert grades. SM318 inserts are excellent for roughing operations and can operate effectively with non-rigid spindles, unstable fixturing setups, and in heavy scale applications. They are recommended for use in moderate speed cast iron milling operations (600-1000 sfm) and light to moderate feedrates (0.004-0.010 ipm).
N/A, P.O. Box 9636, Madison Hts, MI, 48071-9636; phone: 248-589-6267