Westec2000: Hitachi Seiki Introduces Open CNC/PC Network Connectivity
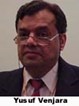
The days when machine tools are designed and built around the control are over, according to Yusuf Venjara, GM-engineering, Hitachi Seiki USA Inc (Congers, NY). The real key to machine tool development today is found in the myriad possibilities that modifying the frontend software bring to communications about the machine tool, its status, and operation.
At Westec2000, Venjara introduced Hitachi Seiki's FlexLink ethernet connectivity for its line of turning and machining centers. Seicos Sigma controls (Fanuc hardware with Hitachi Seiki software) are at the heart of the TCP/IP Internet-enabling protocol that the company has adopted as its machine development strategy for the future.
The Seicos Sigma controls will now feature special software and a Universal User Port (UUP) ethernet connection which provides for bi-directional communication between the CNC machine and an external PC device or PC network.
The implications for users are many. Because the new Hitachi Seiki design uses a standard RJ45 ethernet connection, users can choose from the many options as to what kind of external PC device they might connect to the machine. Connecting to a local office PC network is probably the most likely application. However, it is possible to use Hitachi Seiki FlexLink technology to connect with a hand-held personal digital assistant (PDA) or a laptop computer. It is also possible to use Seiki FlexLink over the internet for remote monitoring and management.
Venjara says their Open CNC architecture is more reliable than competing designs because proven CNC controls (in this case Fanuc) still manage the machines while the open architecture provides for the flow of real time management information about the machine and its production. This avoids any instability, which might be inherent in PC-fused linkages or links dependent upon PC operating systems.
What are the advantages of interactive networking with Hitachi Seiki turning center or machining center? Hitachi breaks them into three categories: Advantages before, during, and after production.
Before production: Seiki FlexLink technology can provide job scheduling and production control. It can access tooling and fixturing databases, verify CAD/CAM—even provide for ordering of tools which will be required. Interactive connectivity can also provide for remote auto tuning for high speed machining.
During production: Seiki FlexLink can provide remote diagnostics and even remote operation. Real-time monitoring of position, program, and displays is possible from any terminal. Event calls can be made by e-mail (alarm, completion and work count), SPC data can be efficiently gathered and remote monitoring at the management and supervisory level is always available.
After production Seiki FlexLink can provide data for productivity analysis along with a permanent record of all machine data before, during, and after completion of the job.
A growing list of third party software is already available to interpret and manage data provided by such real time machine networking and more is sure to come. Hitachi Seiki says what can be done with this new machine-to-network communication is limited only by the imagination of the people who use it and those who can write software to make it work harder. In this respect, Hitachi Seiki is inviting developers to write their own applications for the software.
N/A, 265 Spring Lake Drive, Itasca, IL 60143; phone: 630-250-9000